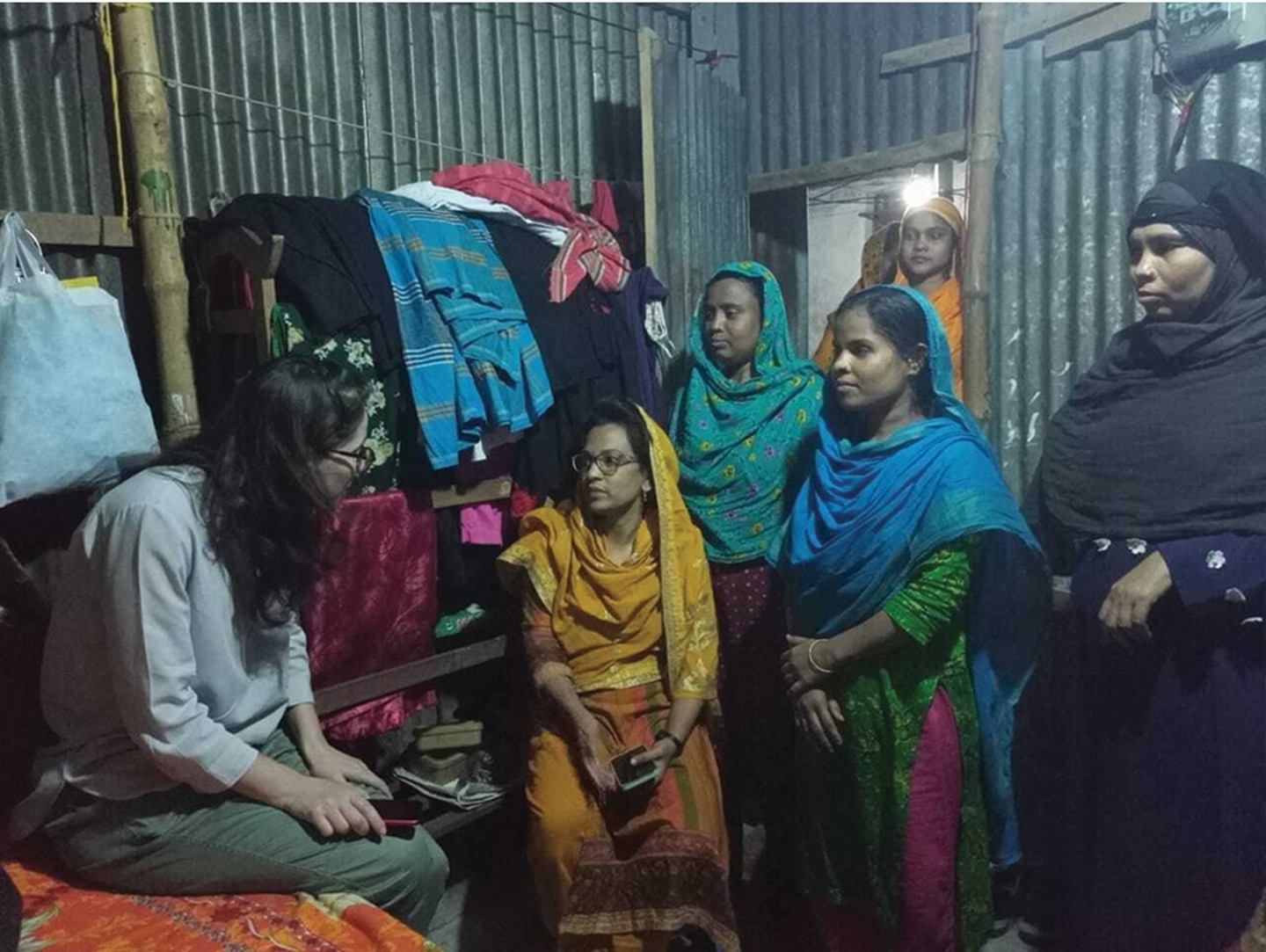
DHAKA, Bangladesh – For the last three months, Rashida Khatun, a garment worker at one of the many factories in Dhaka that make clothes for brands like Primark, H&M and Zara, hasn’t been able to get any overtime.
She used to be able to earn 1,300 taka (a little under $130) a month working extra shifts to supplement her salary, nearly $50 more than the legal minimum. But with economic uncertainty and high inflation prompting consumers to buy fewer jumpers and sweat suits this season, the work just isn’t there.
Nearly a third of what Khatun is still able to earn now goes toward rent for a windowless corrugated iron room with space for little more than a bed, dresser and cupboard for cooking utensils, squeezed down a narrow alley in the northern Dhaka suburb of Uttara. The remainder barely covers monthly spending on essentials like food, which is itself becoming increasingly expensive. When her father-in-law passed away earlier this year, she and her husband couldn’t afford a funeral.
The situation reflects economic pressures ricocheting through fashion’s supply chains, trapping the millions of low-wage workers who power the industry in a crushing squeeze between rising living costs and increasingly precarious work.
Clothing exports from Bangladesh, the world’s third-largest apparel producer, dropped eight percent year-on-year in September and were flat in October. Brands have deferred orders and are pushing for lower prices, while production lines are standing empty, manufacturers said. Meanwhile inflation in the country stands around nine percent.
Like Khatun, many workers relied on overtime to get by even before prices started rising; now, that’s not an option.
Worse Than the Pandemic
Jahanara Begum, a factory trade union president, doesn’t buy meat or fish any more. Without the 50 hours of overtime she’d typically do in a month, she can’t afford to. The room she shares with her daughter, alongside two other families in a three-bed apartment, eats up roughly half her salary.
“How can we live?” she asked over sweetened tea during a recent visit, speaking through a translator. The situation was bad during the pandemic, when brands cancelled billions of dollars worth of orders. But the fallout from the war in Ukraine, which has compounded pressures already facing the market, sending energy and food prices soaring and crimping consumer spending, is like “a second Corona,” one that’s hurting worse, she said.
In more than a dozen conversations in Dhaka earlier this month, garment workers said they were cutting back on basics like food items and tuition and books for their children to make ends meet. They’re worried things will get worse. Some factories have been days, or even weeks, late paying wages owed; others have warned layoffs are coming if demand doesn’t pick up, they said.
Happy Akter, a slight woman who works in quality control at another of Dhaka’s many factories catering to international brands said she’s had to borrow money to make up for the lack of overtime. So far the loans have been small, but she doesn’t know what will happen next month, or if there will be any work at all.
A ‘Holy Shit’ Moment
The current crisis piles more pressure on a workforce with little to fall back on. Chronically low wages leave little opportunity to save for a rainy day and many drew down on whatever they’d put aside just to get through the pandemic. The last three years of disruption squeezed livelihoods in other ways too, increasing incidents of union busting and reducing job security, according to labour rights groups.
Garment workers earn on average roughly half what is required to achieve a decent standard of living, according to a study published by multi-stakeholder advocacy group The Industry We Want in February. The challenge is particularly acute in Bangladesh, where the gap between actual wages and a living wage is among the highest of any major manufacturing hub, it found.
The country’s minimum wage for garment workers hasn’t changed since 2018, when it was increased to 8,000 taka a month, just under $80. It’s due for renegotiation next year, an intensely political debate that will coincide with the run up to the country’s general election.
The tough economic backdrop is likely to make negotiations particularly fraught, with brands pushing for lower prices even as they step up consumer-friendly commitments to decent pay in their supply chains. There’s no consensus yet on how much the minimum wage should rise, but many unions are calling for it to at least double to closer to 20,000 taka.
“This is the time everybody has to be understanding and sensible,” said Faruque Hassan, president of the Bangladesh Garment Manufacturers and Exporters Association (BGMEA). “The industry should increase wages, buyers should not push to reduce prices… and unions should also be sensible… [to not] push so much that [they push workers] out of a job.”
Heading into next year, the industry may face a new source of disruption: labour unrest. And longer-term, climate change looms as a new pressure valve for an increasingly volatile and risky market.
“We’re in a ‘holy shit’ moment,” said Peter McAllister, executive director at the Ethical Trading Initiative, an alliance of companies, trade unions and voluntary organisations that monitors labour standards in supply chains. “People who’ve been in this industry for 30 years [are saying] they’ve never seen a situation so unsure.”
For more BoF sustainability coverage, sign up now for our Weekly Sustainability Briefing by Sarah Kent.