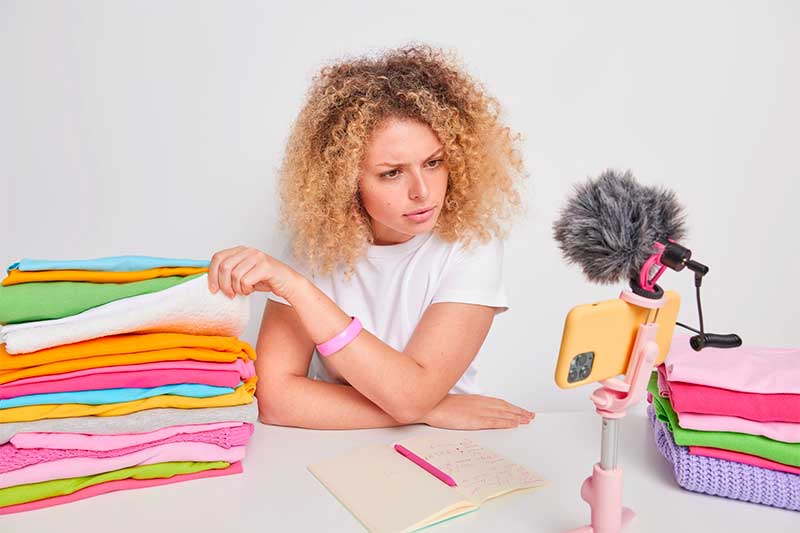
It is a long process from the design of an item of clothing to its hanging in a shopping mall store, and many people are unaware of just how many stages one garment has to go through before it is made available for sale.
The design stage
First of all, a designer has to design the item of clothing, establishing the look, the color, the pattern, and the cut of the garment. This was once done by hand but is mostly done now on a computer using a CAD (Computer Aided Design) system. A sample will be made of the item, often using lesser-grade materials to keep costs down. A panel made up of the designer, the pattern maker, and sewing specialists will then review this sample. They will decide whether the garment is fine as it is or whether any changes need to be made.
Once the item has been approved, the fabrics, trims and buttons, and whatever else is needed are ordered and sent to the factory, along with the production pattern, which details the separate panels of cloth that go into making the complete garment.
Production pattern
This is actually a very complex process involving many steps. Grading is needed to ensure that the pattern will result in different dress sizes. Done by hand, this can be a laborious task, but CAD has made it much quicker. Then the marker maker moves in to measure up all the pattern pieces on the fabric that has been chosen. The marker maker will ensure that he or she has all the necessary pieces while minimizing fabric wastage, and this will tell them how much fabric is needed for the entire production run. Then comes the cutting of the fabric and the sorting of each piece into sized bundles for delivery to the sewing and assembly department.
Quality control
This is a very important part of the production process, as quality control makes sure that the garments produced are fit for sale. Quality controllers will check for open seams, threads that do not match, and missed stitches, among other checks. Once the garments have passed the quality tests, they are sent out for pressing and finishing.
Finding buyers
While all this is going on, the people back in the head office are finding buyers for the clothes. They may already have a buyer before the design process has even begun, but if not, they may have to pitch their design ideas to a number of retailers. They may decide to have an exclusivity deal with one particular retailer or sell to many different stores. They will also work out a price point for each garment, ensuring that they make a profit on each sale.
Logistics
Once the garments are finished, it is time to get them into the stores. A nationwide distribution requires a huge logistical plan involving a fleet of delivery vehicles, like that owned and run by Clarence Gooden, who has worked in the transportation and logistics sector for many years. It is due to his experience and management skills that CSX is ranked as one of the best and largest service providers of freight rail and logistics in the US, with a network that includes 70 ports and 240 railroads. Mr. Gooden also acts as a trade and transport advisor and serves on several manufacturing and transportation boards, as well as the board of the Jacksonville Museum of Modern Art.
The piece of clothing you pick up off the rail in your favorite clothing store has had a long journey before it reaches your wardrobe, with many people working hard to ensure that you have a quality garment to wear to help you look your best.