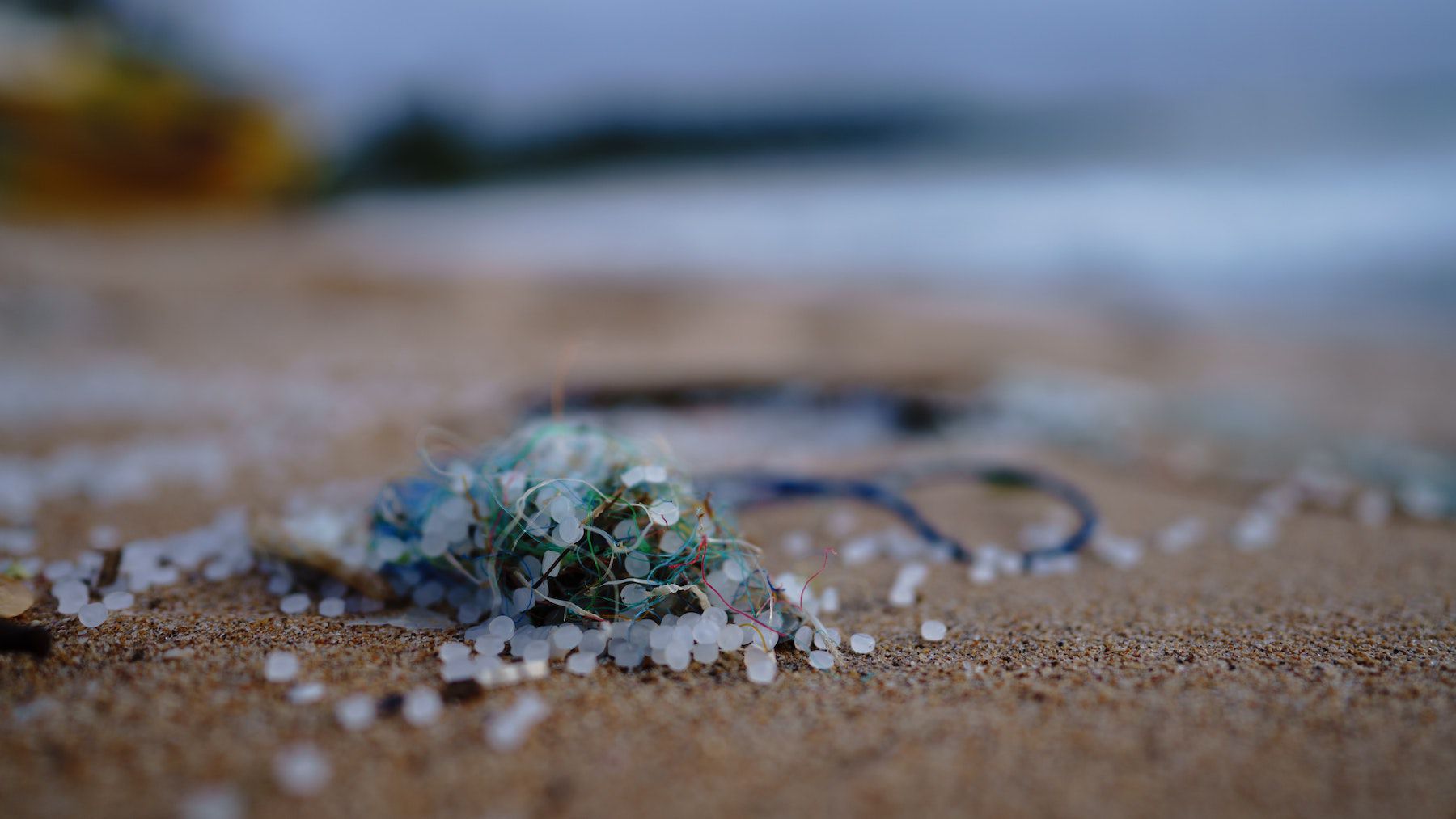
Every year, more than half a million metric tons of tiny plastic fibres leach from our clothes into the environment. They shed mostly in the wash, creating a plastic soup in the oceans and clogging soil. They’ve been found in the food we eat, and even human bloodstreams.
Big brands have responded with a range of products that promise to reduce the problem when consumers wash their favourite yoga pants, fluffy fleeces or woolly jumpers.
Countless retailers now stock mesh bags, designed to capture microfibres released during the laundry cycle. Zara and BASF have created a special detergent that they say reduces shedding by up to 80 percent. Samsung and Patagonia have even developed a new washing machine that reduces microplastic pollution by up to 54 percent, according to Samsung.
But some environmental experts and advocates are questioning the focus on things consumers can do to avoid shedding, rather than on the design decisions that create the problem in the first place.
Brands are “placing the onus on the consumer to do something,” said Karen Sim, senior sustainability strategist at nonprofit sustainability consultancy Forum for the Future, which recently published a report exploring opportunities to reduce microfibre shedding in textile factories. “Of course, consumers should be doing something. But can we actually better understand [the problem] when we’re actually making these products?”
A Material Matter
Tackling microfibres, as the name suggests, starts with examining the fibres, yarns, weaves and knits that go into making a finished garment.
These can have very different properties, with some more prone to shedding than others. As it is, the soaring volume of polyester clothing over the last two decades has left the fashion industry responsible for 35 percent of annual microplastic emissions, according to 2017 UN estimates. Microfibres released from natural materials, like cotton and wool, are also a cause for concern — particularly if dyes or chemical coatings compromise biodegradability.
As attention on the issue has grown, so has the research into the kinds of fibres and fabrics that are most at risk of shedding. The Microfibre Consortium, a group that aims to advance microfibre research and solutions in the textile industry, has built a portfolio of shedding data for over 600 different fabrics. Brands including Patagonia, the outdoorsy label known for its climate activism as much as its fleeces and puffer vests, and sportswear giant Under Armour have also carried out extensive in-house research.
The general takeaway is that using high-quality raw materials is key to reducing the problem. Long-staple cotton fibres, which typically retail at a premium, are less likely to break away than shorter ones, for instance. For synthetics like polyester, high-quality plastic pellets are key, said Matt Dwyer, VP of product impact and innovation at Patagonia. And when it comes to recycled textiles, long filaments extruded from chemical recycling are preferable to mechanically recycled materials, which are typically chopped up into short fibres before being re-spun, he added.
How the material is treated and processed is also important to avoid weakening fibres in a way that makes them more susceptible to shed, said Lewis Shuler, head of innovation at Alpine Group, a textile supplier for brands including the North Face, American Eagle Outfitters and Under Armour. “You don’t want mechanical processing that’s going to break the fibre,” he said.
As a general rule, avoiding fleece, or fabrics that are stretched and brushed to create a velvety-soft finish known as “peaching,” is a “no-brainer,” he added.
Some brands, however, have found complications to this rule of thumb: According to Dwyer, a well-made brushed polyester fleece created from recycled plastics can shed as little as a tightly woven nylon used to make Patagonia’s waterproof vests.
“Oftentimes, we’re wired to reduce these complex problems to … simple answers,” said Dwyer. “Really, there’s a whole lot of nuance.”
Better Construction
Choosing the right material — while important — is not the only creative choice that can help prevent or reduce microfibre shedding. How a garment is constructed also has an important role to play.
“A major source of the uncontrolled release of these fibres tends to be at the seams,” said Edwin Keh, chief executive of public research institute The Hong Kong Research Institute of Textiles and Apparel (HKRITA). Raw, unfinished hems are prone to fraying and breakage, meaning fibres can easily come loose.
That’s something relatively simple to tackle using existing production techniques, experts say. Apparel makers can take cues from the outerwear industry, which often uses ultrasonic or heat welding to seamlessly assemble waterproof jackets, said Keh, though this would require expensive specialist equipment not available in most cut-make-sew facilities. Other options include adhesive taping, better stitching finishes, or even using lasers instead of scissors to cut out clothing patterns in factories — all of which can help smooth off raw edges with loose fibres.
With many of these easier fixes, “it’s just [a question of] getting the brands to understand it’s worth the extra 10 cents,” said Shuler.
Industrial Washing
Before textiles ever make it into consumers’ washing machines, they go through an industrial washing process that is itself responsible for a significant amount of microfibre shedding.
Textile manufacturing releases 120,000 metric tons of synthetic microfibres per year, compared to 530,000 metric tons at the consumer-use phase, according to a 2021 report released by environmental organisation The Nature Conservancy and consultancy Bain & Company, meaning that for roughly every 500 t-shirts manufactured, one is lost as microfibre pollution.
Companies could bring down these volumes by reducing water usage and temperatures during wet processing and dyeing, but with the technology currently available that can lead to compromises on quality and consistency in the finished products, according to research carried out by Forum for the Future and Singapore-headquartered textile group Ramatex.
This is where lower-impact dyeing innovations, such as waterless printing, supercritical CO2 chambers (which use dyes dissolved in gas, not water) or dope-dyeing (which injects pigment into synthetics at the plastic-pellet stage), could be transformational in reducing microfibre pollution at the manufacturing level, the report found.
There are also innovative solutions geared at strengthening the textiles themselves, like material science company Pangaia and MTIX’s laser surface treatment, designed to reconstitute fibres to stop them from breaking away.
But investing in new technology is risky and expensive. Suppliers are often expected to shoulder the costs themselves, even just to carry out in-house testing. For instance, a launderometer, which can measure fibre shedding alongside performance metrics such as colour-fastness, costs about $25,000, said Shuler. Even basics like wastewater management, which could help factories collect (and even recycle or repurpose) fibre pollution, require investment in infrastructure and robust standards across the board.
Nonetheless, useful innovations to help factories and regulators could soon be on the way — from plastic-eating enzymes to retrofitted pipes for collecting microfibres. HKRITA, for example, is in the process of scaling up its “acoustic sweeping” technology — a T-shaped pipe that generates soundwaves to “push” microplastics into a collector — so it can be retrofitted to industrial and municipal water systems. It’s also less expensive and energy-intensive than current filtration technologies, said Keh.
Ultimately, fashion needs to accelerate progress beyond the research and testing phase to implement solutions beyond consumers’ laundry habits. As Forum for the Future’s latest report notes, better material and production choices should help reduce microfibre emissions at the consumer-use phase, and looming regulation in the EU will put the onus on brands to develop durable clothes with a smaller environmental footprint, as well as complying with measures to tackle microplastics.
“We’re not waiting for perfection, we’re rolling out improvements,” said Keh. “Otherwise we’ll be in the labs forever.”